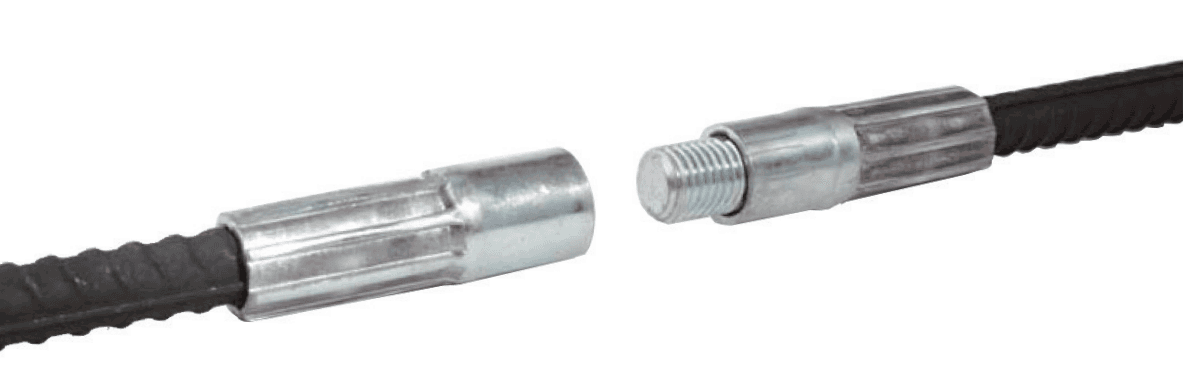
Bartek BP Rebar Splice System
Combining our state of the art crimping technology and BP series couplers, SRG have developed our own hydraulic crimping machine to swage our couplers onto the rebar. The process compresses the coupler around the profile of the rebar and embeds itself into the rebar ribs cutting into the coupler material to create a secured mechanical interlock, which does not reduce cross-sectional area.
Crimping Machine
The crimping tech is the key of the system, instead of using a 3rd party universal-purpose press (mostly crimpers for hose industry), we developed our own crimping machine which makes the crimping much
faster and most of all much more accurate. The Precise metering system controls the crimping accuracy to 0.1 mm for the best interlock between the rebar and the coupler, combining the improved coupler material property, our system ensures the high performance as well as reliability.
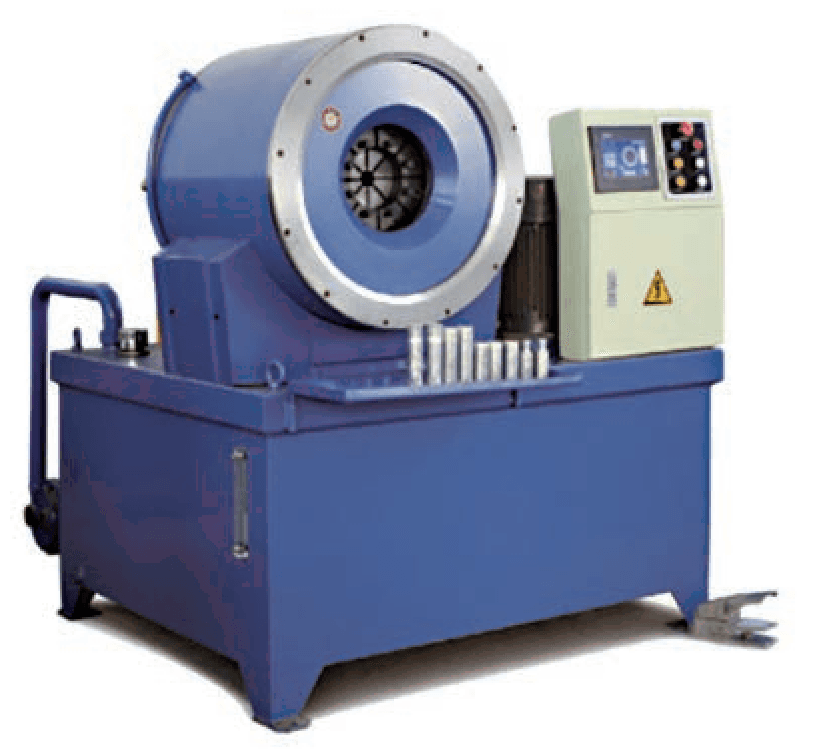
Figure:
Crimping Machine
4th Generation Crimping machine
• Improved crimping mechanism greatly increases the pressing precision.
• Max. 2,500T crimping force completes the crimp of a 40mm rebar coupler in 15 sec.
• Accurate Crimping thanks to the precise metering system.
• Easy dies change thanks to the programed data for all sizes and types of couplers.
Easy pre-fabrication
• No painful thread cutting or rolling on the rebar any more.
• Just a clean and precise crimp completes the splice preparation.
• Screw the male bolt into the female, no torque wrench required.
Quality assured
• Manufactured under strict quality assurance plan, ISO 9001 certified.
• Full traceability of the couplers in production.
• Full traceability of each crimp on the crimper, records can be export for QC.
Features
1. Live crimping monitoring. The crimping dimensions are measured live, warning will be given immediately if the crimped dimensions fall out of the required range.
2. Position of the rebar stopper is servo-motor driven and software controlled, no more manual adjustments needed, higher efficiency.
3. Simple operation, quick to switch from one size to another thanks to the pre-set data in our smart crimping database, just change the dies and rebar stopper while all the other adjustments such as the positioning and crimping force are all set by software.
4. Powerful and quick crimping, the crimping for 40mm rebar takes only 15 seconds.
5. Improved crimping mechanism, the crimping movement is well controlled in its path and the crimping force is evenly distributed, higher pressing precision.
6. Optimized hydraulic system, reduced cycle time for each crimping.
7. V shape dies ensure the pressing force is in the center of the pressing mechanism, better pressing performance and longer life of dies.
8. Data input and adjustments all on touch screen, live animation of the crimping process.
9. Full traceability: the crimping data of each coupler is stored in the system and easy to export via data cable or Internet.
Description | Data |
---|---|
Crimping Performance | |
Crimping Force | 2500 Tons (max.) |
Outer diameter of couplers | Ø16-Ø70 |
Rebar sizes | 10mm to 40mm |
Hydraulic System | |
Hydraulic work pressure | 25 Mpa (max. 31 Mpa) |
Pump Motor | 11 kw |
Oil Type | 46# Hydraulic oil |
Oil tank volume | 800 L |
Cooling system | Air cooling and water cooling |
Automation & Software | |
Crimping force control | Automatic |
Crimping Dimension control | Automatic |
Position stopper for coupler and rebar | Automatic |
Crimping records | Up to 10,000 records |
Firmware & software update | Via Internet with 4G module |
Miscellaneous | |
Power supply | 380V/50Hz |
Machine weight | 2300 kgs (without oil) |
Machine dimensions | 1610 x 1370 x 1480mm |
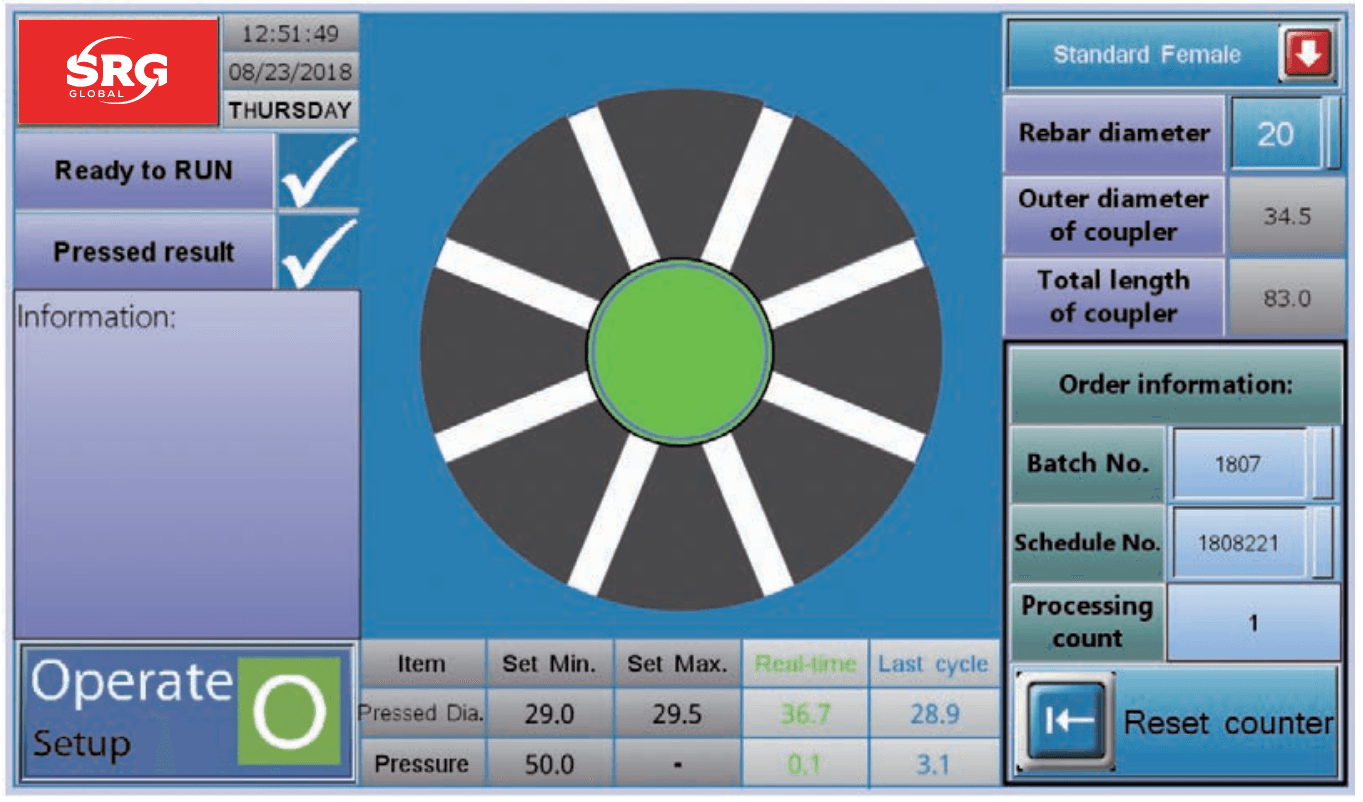
Figure:
Interface
Software Highlights
1. To switch from one type or size of coupler to another, just choose the desired type and size then all the setup required will be displayed to guide the operator to set up the machine correctly.
2. For each crimping, the live crimping process is displayed and the crimping result will be verifed, if failed to meet the range required, warning will be given.
3. Crimping records are stored with all the information for each pressing, including the batch No., work No. and crimping results. The data can be export to keep a good track of all the jobs.
4. Special requirements of our customers can be easily addressed by remote frmware update in case any new demand requested.